COATING TECHNOLOGY
High performance down to the last nanometer – layer by layer
The right coating can increase performance and cost effectiveness:
H-O-T offers the full range of technologies. In addition to standardized applications, we will also work with you to develop a customized solution – tailored exactly to your own requirements.
Take advantage of our 30 years of expertise, impressive innovations and valuable expert knowledge about practical uses. We guarantee reproducible quality for every coating – as well as the entire H-O-T service package, of course.
PVD coatings
PVD (Physical Vapor Deposition) stands for the physical deposition of thin layers from the vapor phase.
This process produces layers with a high proportion of covalent bonds of the layer atoms. Properties such as hardness and thermal and chemical stability are significantly enhanced by the PVD coating of precision tools and high-quality components. At the same time, properties such as the coefficient of friction and the tendencies to jam, clog, stick, corrode and oxidize are significantly reduced. Our high-tech coatings have been used in all sectors of industry since 1988.
PACVD coatings
PACVD (Plasma Assisted Chemical Vapor Deposition) is a development of the CVD process and combines the advantages of both the PVD and the CVD process. In the PACVD process, the coating is deposited by a chemical reaction from the gas phase at temperatures below 180°C with a specific plasma support.
Area of application
SHAPING AND STAMPING TECHNOLOGY
Advantages:
- Low tendency to build-up
- Significantly longer service life
- No sticking and cold build-up
- Optimization of the flow characteristics
- Clean cuts and therefore less dressing needed for the work-piece
- Reduced coefficient of friction and therefore reduction in the stamping and retraction forces
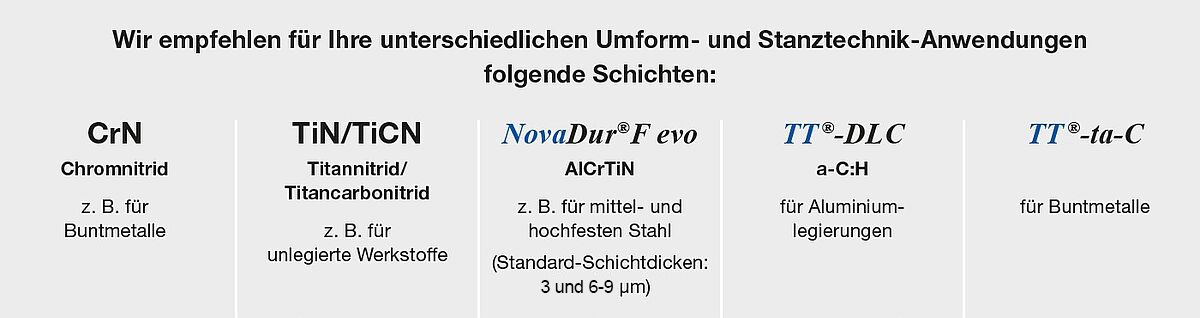
Area of application
PLASTICS TECHNOLOGY
Advantages:
- Excellent wear protection
- Protection of structured tools and protection against damage to finishes
- Improved demolding properties
- Faster filling > shorter cycle time
- Reduced cleaning through reduction of plate-out
- Increased production reliability
- Improved surface quality of the plastic parts
- Reduced distortion of the plastic parts
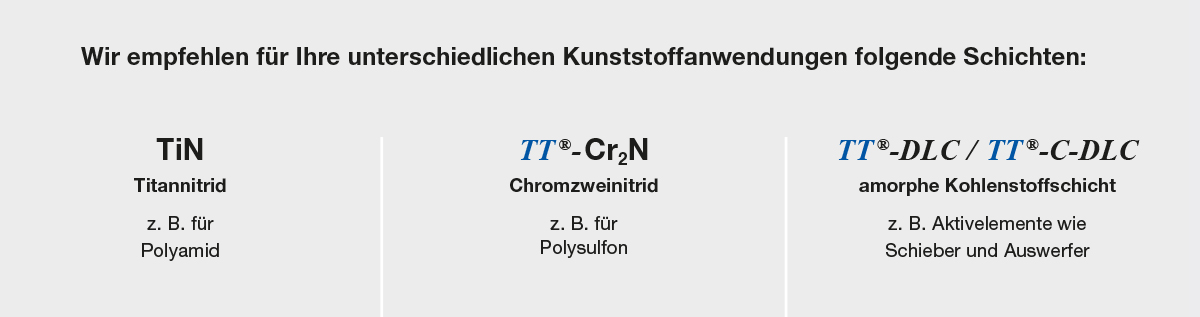
For more efficient milling, stamping, cutting, …
NovaDur® Prime (AlCrN) can be used anywhere, and it optimizes manufacturing reliability in soft and medium-hardness materials.
- Significantly longer service life thanks to excellent resistance to wear
- Extreme temperature and oxidation resistance when wet or dry machining
- Improved productivity and cost effectiveness due to faster cutting speeds
TT®-DLC
TT®-DLC is a metal-free diamond-like layer of carbon and is deposited at low temperatures using the PACVD process. The combination of good wear-resistance and outstanding frictional and non-stick properties makes TT®-DLC coatings an ideal surface treatment for components and tools subject to high frictional forces.
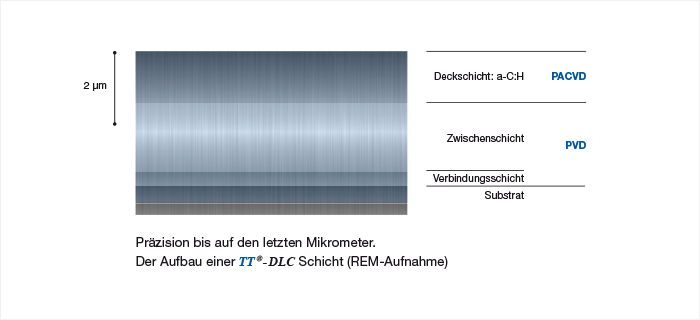
TT®-C-DLC
TT®-C-DLC coatings are a sub-group of the amorphous, diamond-like carbon coatings (DLC – Diamond-Like Carbon). Unlike the majority of the commercially available TT®-DLC coatings, they are not deposited from gaseous hydrocarbons (e.g. acetylene or methane) using the plasma-activated CVD process (PACVD – Plasma Assisted Chemical Vapor Deposition).
TT®-C-DLC coatings can achieve both a higher hardness and a lower coefficient of friction than the TT®-DLC coatings deposited by the PACVD process. The properties of TT®-C-DLC coatings are summarized in the table.
TT®-C-DLC coatings are normally deposited with a thickness of 1.5 ± 0.5 μm. Because of their properties, these coatings are often used for standard components.
TT®-TA-C
TT®-ta-C coatings are a sub-group of the amorphous, diamond-like carbon coatings (DLC – Diamond-Like Carbon).
TT®-ta-C is a tetahedral, amorphous, hydrogen-free carbon coating that is produced from solid carbon (graphite) by means of laser arc technology (PVD process).
Coating structure: | Hydrogen-free, tetahedral, amorphous carbon, sp³ content adjustable above 85 % |
Hardening: | 4500–7000 HV, adjustabl |
E-modulus: | 300–450 GPa, adjustabl |
Coefficient of friction: | 0.05–0.10 (dry on steel) |
Wear coefficient: | 1*10-8 mm³/Nm (dry on steel) |
Temp. resistance: | 400– 500°C in air, <800°C in vacuum |
Coating thickness: | bis 1,5 μm |
Reliable high quality over a long period:
hi-Fusion significantly improves the surface hardness – enabling you to win the struggle against wear. It also prevents the mold surface from being scratched, as well as the edges from becoming brittle and the plastics from sticking to the tool. Using hi-Fusion also saves you time and money in post-treatment.
Experience coating technology that is more advanced than ever.
hi-Fusion is a plasma-supported diffusion process for the targeted optimization of mold surfaces (in plastic injection molding) in series production.
hi-Fusion in practice
Hard facts to put you one step ahead ...
- Improves scratch resistance
- Increases wear resistance
- Raises corrosion resistance
- Improves polishing ability
- Reduces maintenance costs
- Extends service life
- Ensures consistent quality
Production details
Suitable materials: | 1.2343 | 1.2344 | 1.2379 | 1.2311 | 1.2738 | 1.2083 (vergütet und angelassen > 420° C) |
Surfaces: | Polished and structured surfaces |
Delivery condition: | Metallically bright and disassembled |
Coating systems: | Combination with PVD and PACVD coatings possible |
Machine size: | ø 1.200 x 2.400 mm (other dimensions on request) |
Individual weight: | Max. 5 metric tons (other weights on request) |
After-treatment: | Possible |
Talk to us.
We’ll be happy to advise you.
T: +49 (0)911 36014-1042
hot-nuernberg@hot-online.de